1.1.1 Introduction
① Location of applet configuration settings

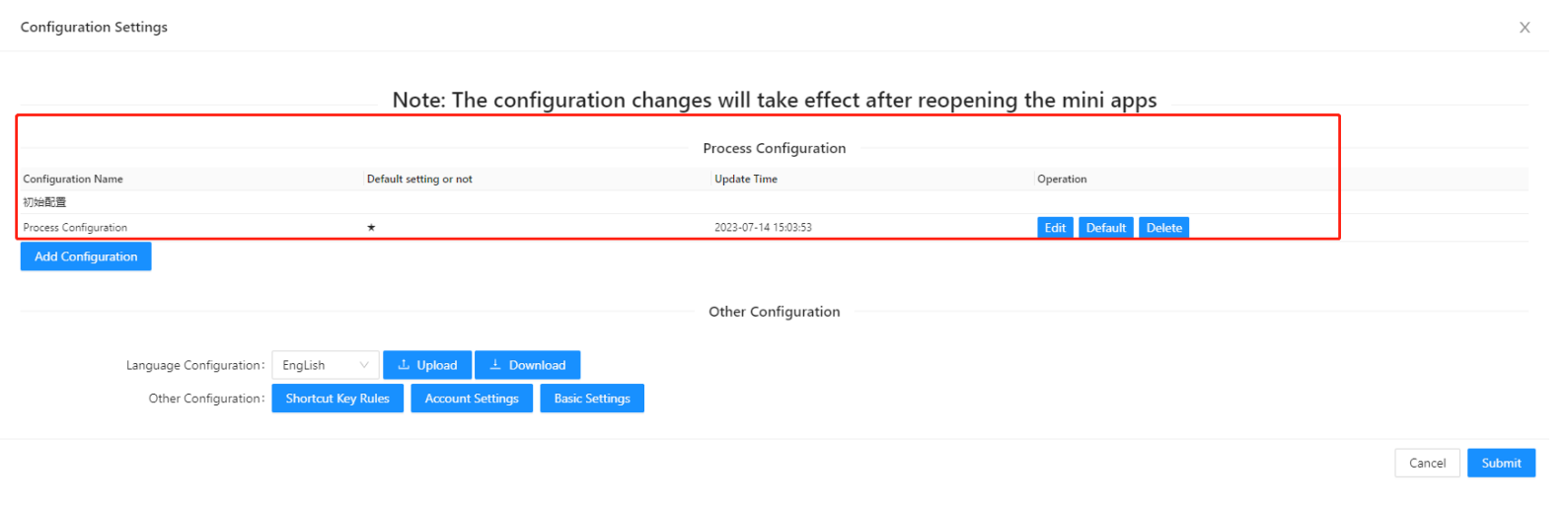
Note: Multiple sets of factory process configurations can be configured under the same account
1.1.2 Configuration Relationship Introduction
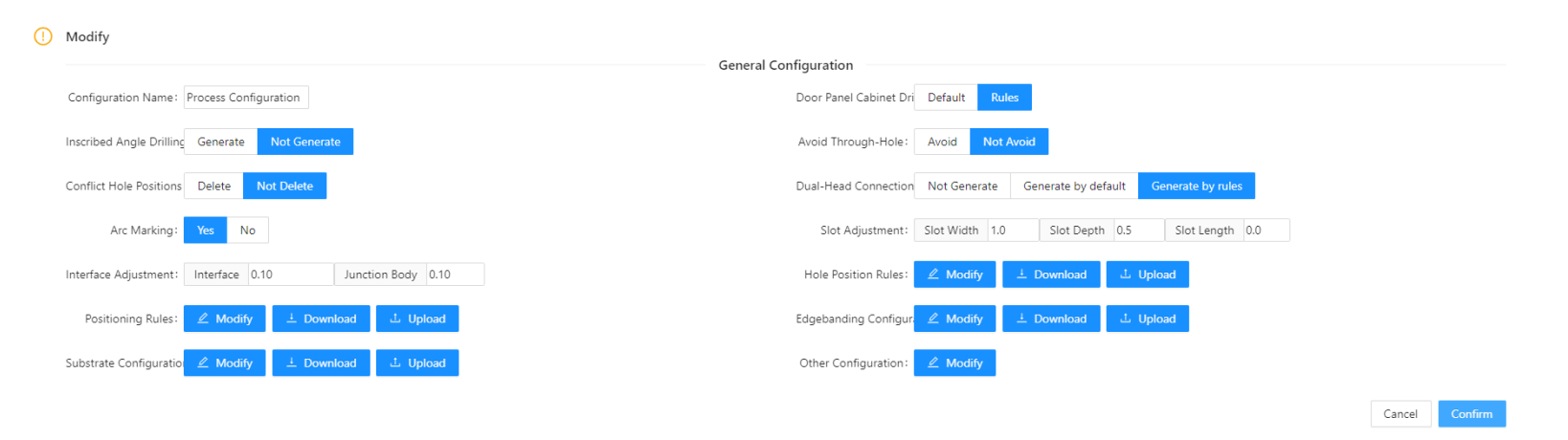
① General Configuration: Except for hole position and edge banding, other process setting positions are independently configured;
② Hardware Accessories Setting: The defined position of all connected hardware holes is independently configured and can be downloaded and uploaded;
③ Hardware Hole Layout Rule: The data association position between the Coohom and Applet models is independently configured and can be downloaded and uploaded.
④ Edge Banding Setting: The data association position of edge banding for the Coohom and Applet models is independently configured and can be downloaded and uploaded.
Note: The connection name in ③ should be consistent with the name in ②. For details, please refer to section 3.5 below.
2、Hardware Fitting Settings
1.2.1 Position
Click on "Modify" to enter the configuration.
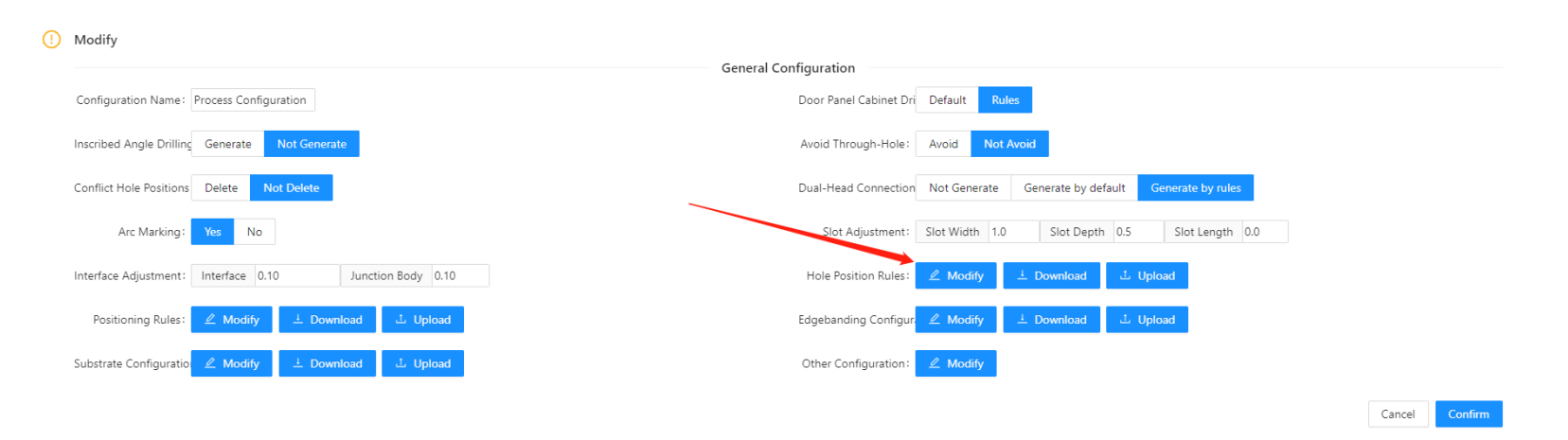
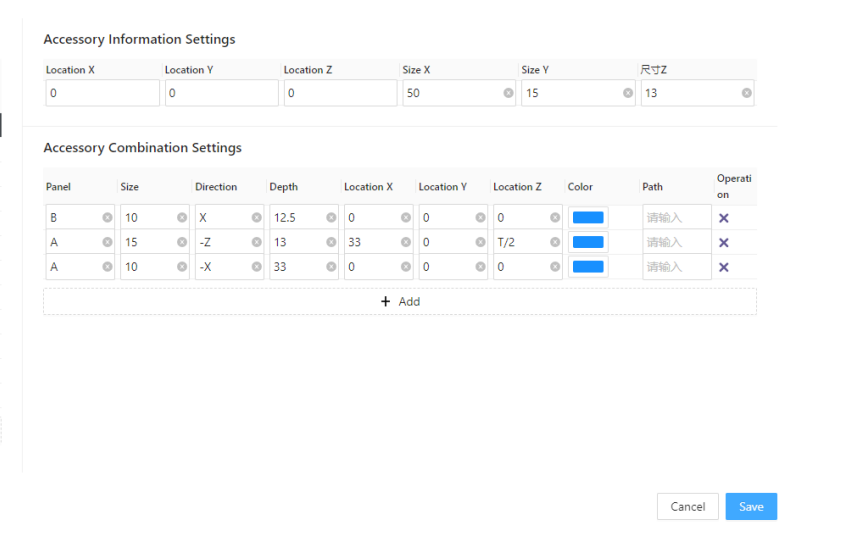
1.2.2 Fittings List
This is primarily used to configure hardware names, display hardware models in the applet, include hardware data in the material list, and provide various other capabilities required in the industry.
For more details, please refer to the content in the table below.
Content List
Fill in Content
Function Details
Fittings
Fill in connection name
The final name will be output as the hardware name in the material list, and it will be called in the hardware hole layout rule to establish the association with the hardware.
Hardware
Fill in the hardware ID
In Coohom, each model will have a unique ID that can be associated here. The applet will eventually call this model for display, and it has specific requirements for the modeling coordinates of hardware models.
Note① :This hardware is only used for disassambly applet display and does not serve as any data or information processing output.
Note② :In this table, the ID column for hardware must not contain duplicate values.
Virtual Hardware
Fill in the virtual hardware ID
In Coohom, each virtual hardware has a unique ID that can be associated here. If this field is filled in applet, it will be recognized as an input and used to calculate the quantity for output.
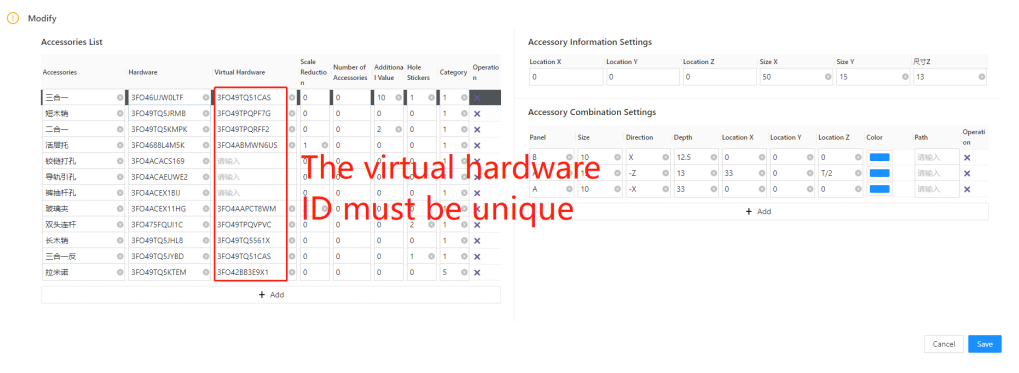
Note:In this table, the ID column for virtual hardware must not contain duplicate values.
Reduce size
Enter reduced size
It is generally used for movable layer boards and glass layer boards. If you input "1" in this field, when generating the cutting list data, the system will deduct the specified reduction value from the four edges of the connected panels. The reduction value will not be applied to edges that do not have connections.

Configuration:
In the hole layout rules, the name preceding the EC value must be identical to the hardware name in the component positioning list. Otherwise, it will become invalid.
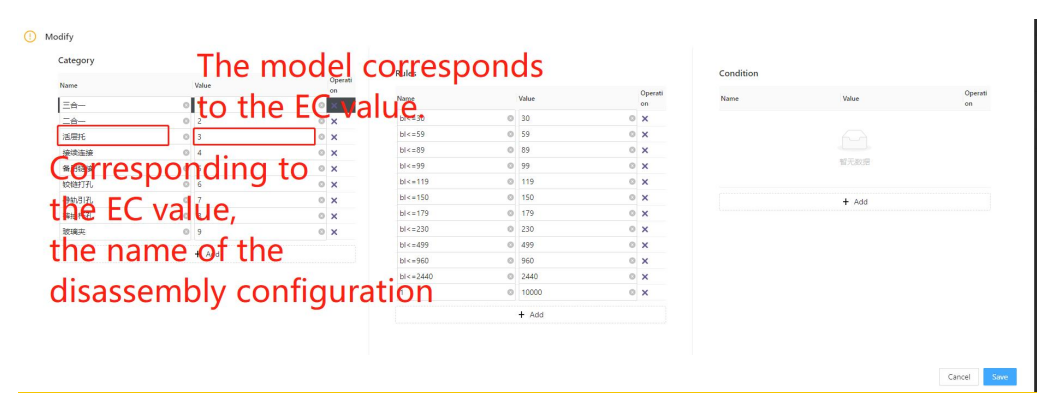
Additional Quantity
Fill in additional quantity ratio
In the industry, there are cases where extra hardware fittings are added during distribution. You can simply enter the corresponding ratio here.
For example, if you want to add one extra for every 10 hardware fittings, you can directly write "10". In the final materials list output, for every 10 hardware fittings, one extra will be added. If there were initially 100 fittings, the output will be 110.
Adhesive
Filling coefficient
As shown in the figure, the number of adhesive is filled in 1, and the number of three-in-one in the final hardware single will output the corresponding multiple of adhesive
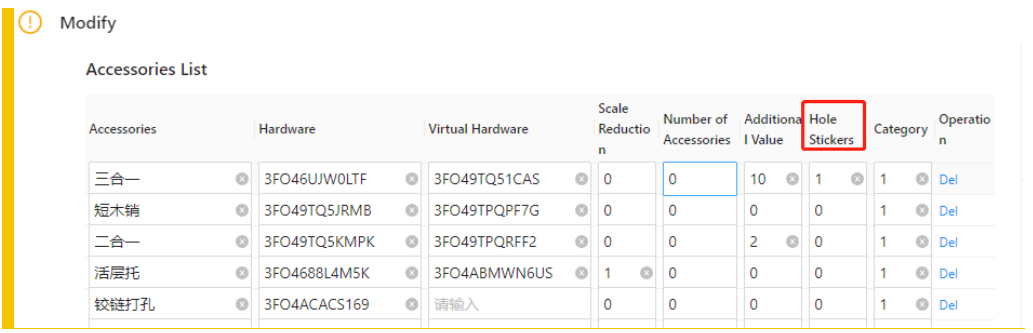
Type
Value:1:2:3:4:5
The type in this section primarily controls the hardware, and how to applet processes data. For all connector types, such as three-in-one or two-in-one, you can fill in the value "1".
value "2":represents a square slot. For more details, please refer to the hardware slot configuration below (1.3).
value "3" represents a circular slot. For more details, please refer to the hardware slot configuration below (1.3).
value "4" represents an irregular slot. For more details, please refer to the hardware slot configuration below (1.3).
value "5" represents invisible parts. For details, see the following hardware slot configuration (BOM version removal capability).
1.2.3 Fittings Information Setting
①Description
This position is primarily used for adjusting various types of hardware in the display position within the model, along with additional depth for specific types.
Note:Additional depth for specific types refers to the values mentioned above, such as 2 (square groove) and 3 (circular groove) scenes, which can be viewed based on the hardware groove in section 1.3This position is primarily used for adjusting various types of hardware in the display position within the model, along with additional depth for specific types.
② Position XYZ
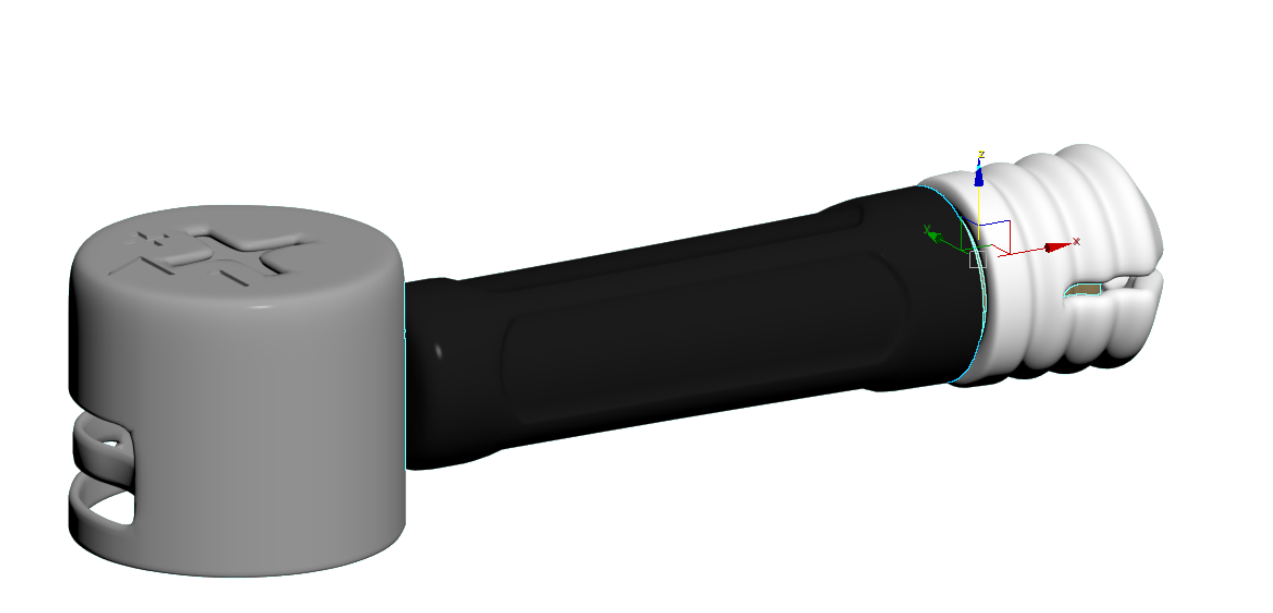
-
As shown in the above image, there are specific requirements for the coordinates when creating our models from 3dMax. During the three-in-one installation, the white pre-embedded component is placed above the side panel, while the black connecting rod is installed above the horizontal board. Therefore, the center point needs to be set as the origin between the black and white components in 3dMax.
As shown in the above image, there are specific requirements for the coordinates when creating our models from 3dMax. During the three-in-one installation, the white pre-embedded component is placed above the side panel, while the black connecting rod is installed above the horizontal board. Therefore, the center point needs to be set as the origin between the black and white components in 3dMax.
-
We have completed the above tasks, including model upload, ID filling, and specifying the type. However, for certain hardware components such as two-in-one or movable shelf pins, they are not located at the center of the side panel during installation process. Despite this, when we upload the model, it already has an origin point defined. Therefore, we need to make some position adjustments for these types of hardware components, as shown in the image:
We have completed the above tasks, including model upload, ID filling, and specifying the type. However, for certain hardware components such as two-in-one or movable shelf pins, they are not located at the center of the side panel during installation process. Despite this, when we upload the model, it already has an origin point defined. Therefore, we need to make some position adjustments for these types of hardware components, as shown in the image:
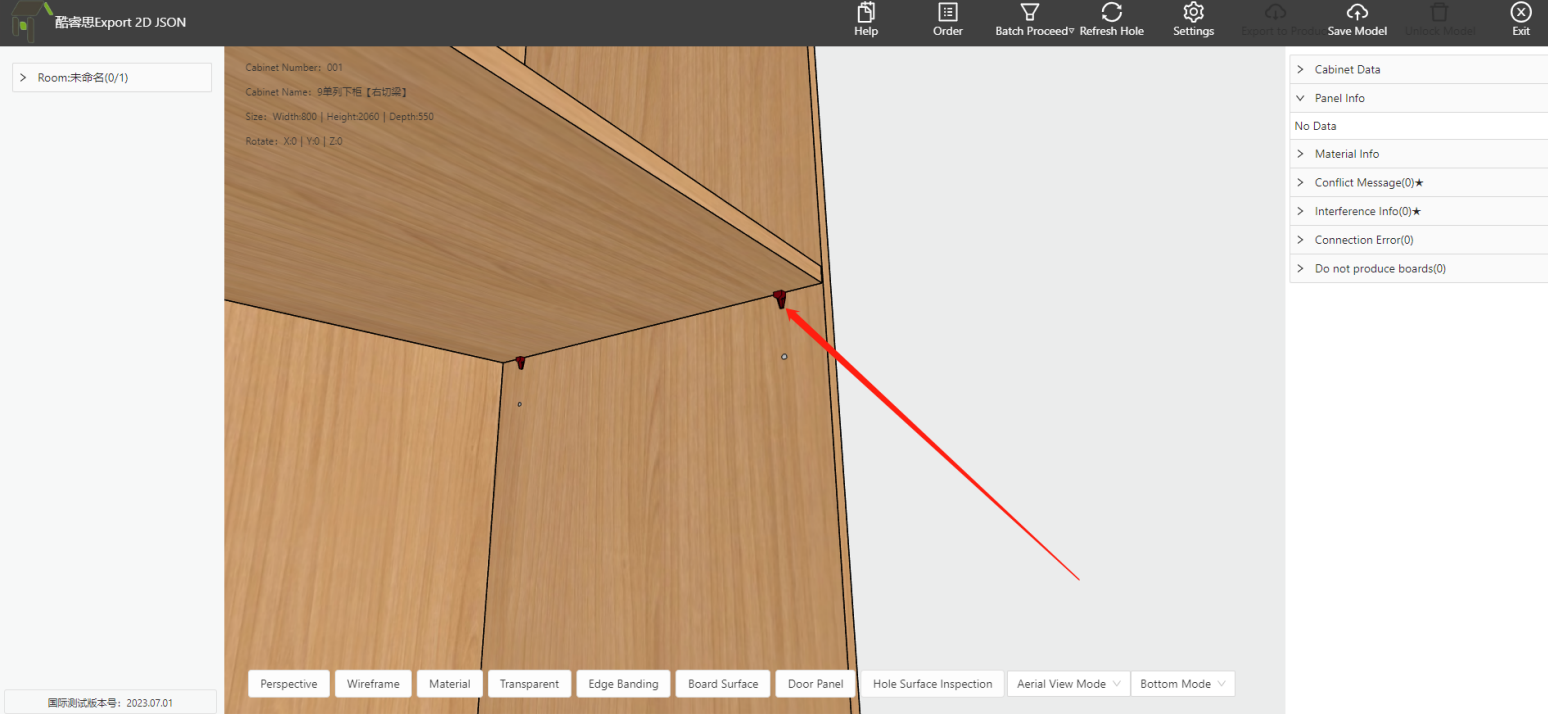
-
The correct installation method for this hardware component is below the panel, so we need to move it along the Z-axis to achieve the desired effect. Please note that the displayed model effect does not represent the actual position of the holes.
The correct installation method for this hardware component is below the panel, so we need to move it along the Z-axis to achieve the desired effect. Please note that the displayed model effect does not represent the actual position of the holes.
③ Size XYZ
l The values of dimensions X, Y, and Z will be written into the bill of materials (BOM) as specifications for this structural hardware. The subsequent material list can obtain the specifications of the structural hardware based on the data from the BOM.
1.2.4 Fittings Combination Settings
1.2.4.1 Description
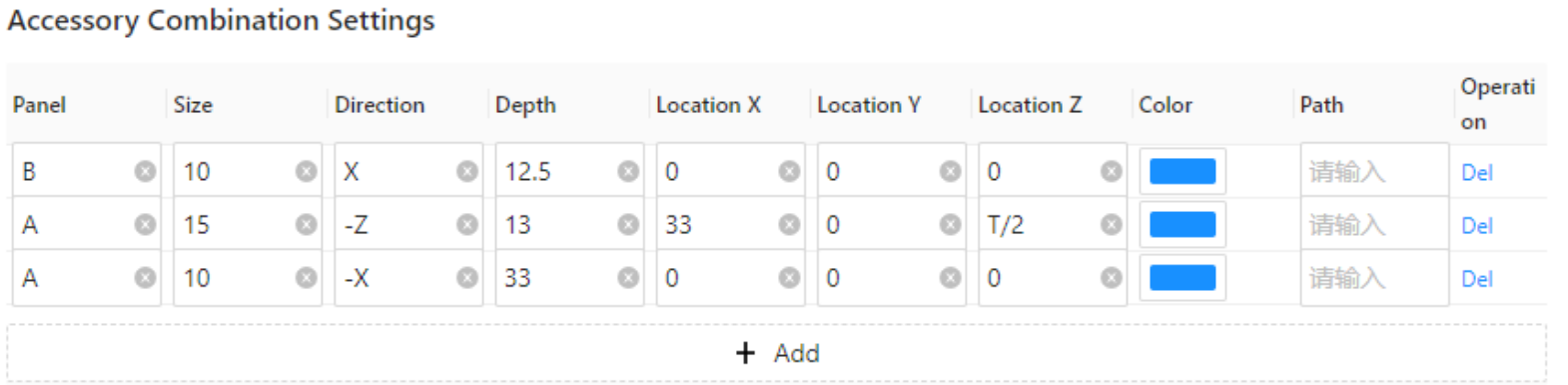
-
In the industry, there are various types of cabinet connecting hardware, and it is common for each hardware component to undergo a processing step that involves multiple surfaces and hole configurations. For example, in the case of a three-in-one configuration, we would need to set lock plate holes and side panel connecting rod holes on the active board, as well as plug holes on the passive board.
In the industry, there are various types of cabinet connecting hardware, and it is common for each hardware component to undergo a processing step that involves multiple surfaces and hole configurations. For example, in the case of a three-in-one configuration, we would need to set lock plate holes and side panel connecting rod holes on the active board, as well as plug holes on the passive board.
1.2.4.2 Connecting Hardware Definition
-
Connection Fittings Definition
Connection Fittings Definition
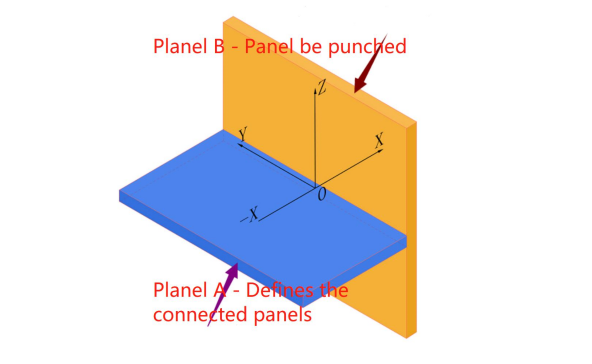
1. The definition of fittings uses a Cartesian coordinate system in three-dimensional space, as shown in the figure above.
2. As shown in the image, A and B are used to represent panels. In this case, A represents the defined connecting panel, while B represents the panel that generates the perpendicular hole. Taking the three-in-one connection as an example, A is defined with a 15mm fastener hole and an 8mm horizontal linkage hole, while B is defined with a 10mm plug hole in the vertical direction.
3. The program generates the connection by default during the design process.
4. It is recommended to first define the vertical holes drilled on panel B.
5. The hole positions defined on the A are based on the initial state of the panel, where the panel is neither rotated nor moved. The thickness of the A is denoted by T by default.
③ Size
-
On panel A or B, the diameter of the drilled hole.
On panel A or B, the diameter of the drilled hole.
④ Direction
-
Define the direction of the drilled hole's exit, determining the direction in which the hole's depth is increased.
Define the direction of the drilled hole's exit, determining the direction in which the hole's depth is increased.
⑤ Depth
-
Based on the above size and direction, customize the punching depth value
Based on the above size and direction, customize the punching depth value
⑥ Position x、y、z
-
Combined with the definition picture of the above connector, the hardware locates the center of the hole surface with 0,0, and Z determines the offset distance of the hole surface
Combined with the definition picture of the above connector, the hardware locates the center of the hole surface with 0,0, and Z determines the offset distance of the hole surface
1.2.4.3 Offset in the thickness direction of the Z component for side holes.
l In the industry, cabinet panels are generally classified into specifications with thicknesses of 18mm, 25mm, and 36mm. In production, different manufacturers have their own process requirements. For example, for a 25mm thick panel, a three-in-one connection may require a 9mm hole offset, while some 25mm panels may require centered drilling. Therefore, in such cases, it is necessary to make adjustments for connection hardware based on different panel thicknesses. For more detailed information, please refer to:
① Common Situation
a. For 18mm thick panels, the standard practice is to drill holes in an evenly distributed manner, which is the most common and standardized process in the industry.
b. For 25mm thick panels
they can be categorized based on different requirements:
l - Centered drilling: With centered drilling, the side holes are typically located at the center position of the panel thickness. The depth of the lock pin hole is generally (thickness/2) + 4.5.
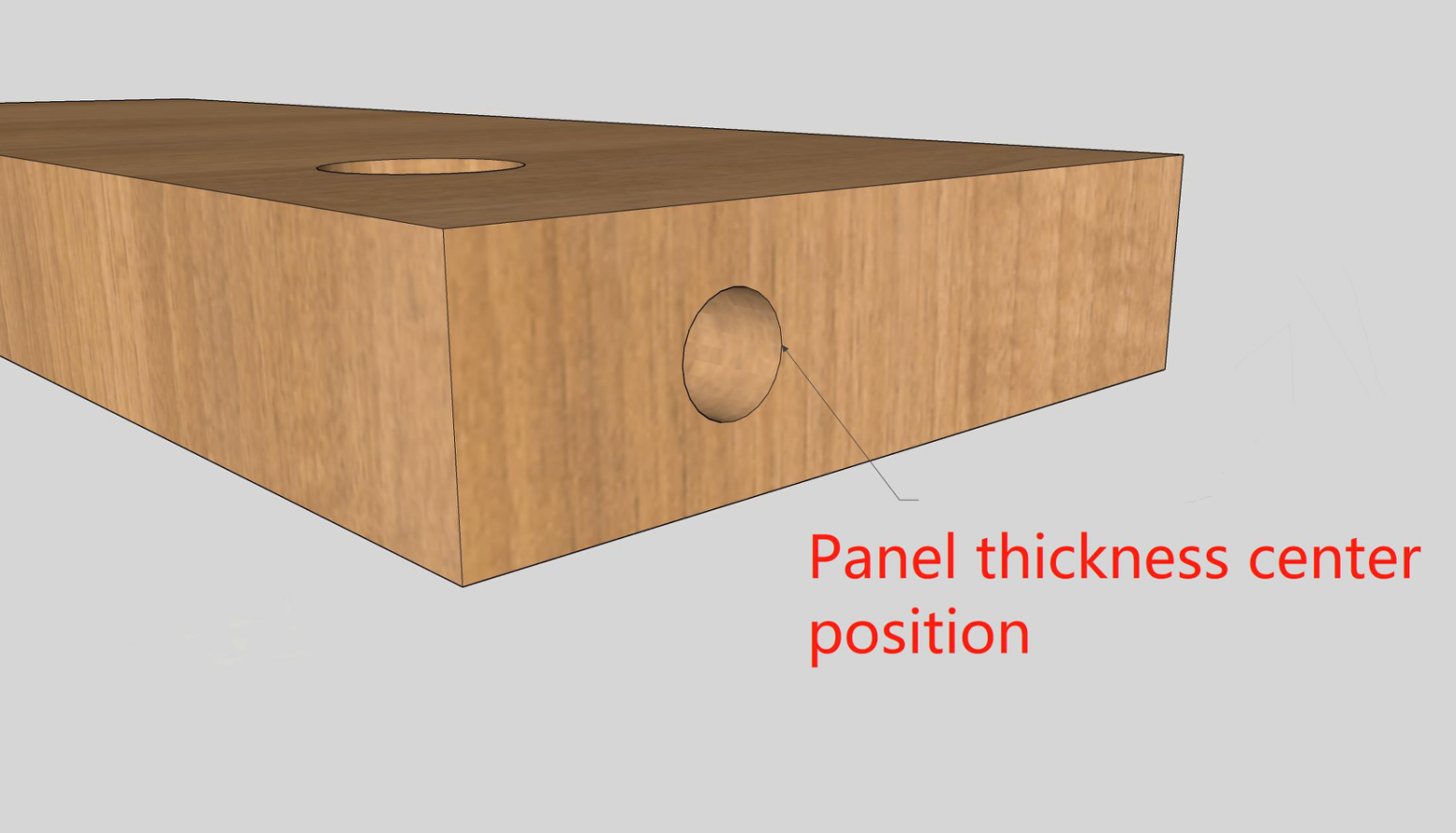
-
Drilling with a 9mm hole offset: A 9mm hole offset means that, with the exit face as the reference, a side hole is drilled at a position 9mm below. The depth of the lock pin hole remains the same as that for the 18mm thick panels, which is approximately 9 + 4.5.
Drilling with a 9mm hole offset: A 9mm hole offset means that, with the exit face as the reference, a side hole is drilled at a position 9mm below. The depth of the lock pin hole remains the same as that for the 18mm thick panels, which is approximately 9 + 4.5.
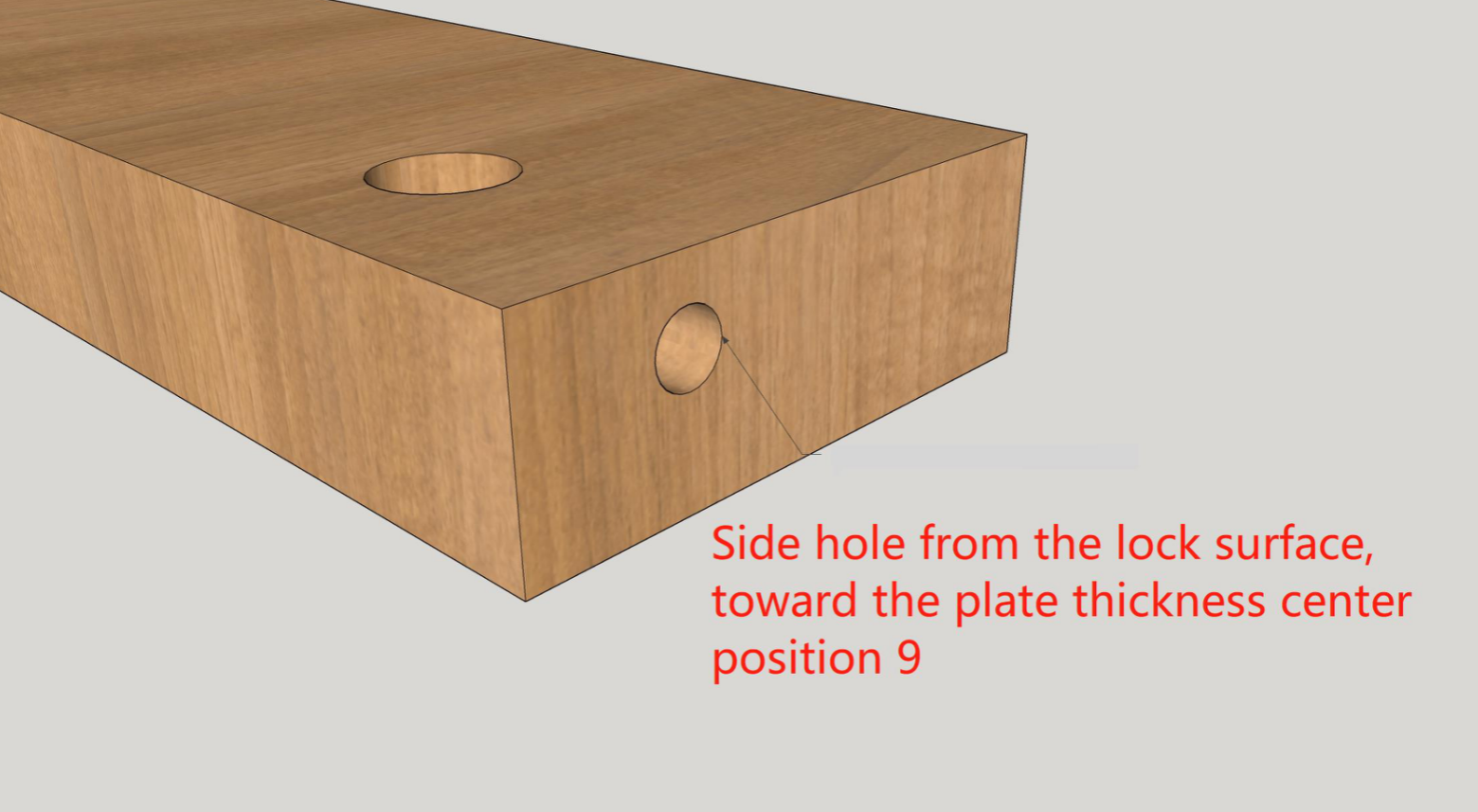
c. The same principles of 36mm and 25mm thick panels. When drilling with centered holes, the depth of the lock pin hole is approximately around 22mm.
Note: Regardless of the position of the side holes on the active panel, the hole positions on the passive panel need to be perfectly aligned with the center of the side holes on the active component. Therefore, it is necessary to configure the settings in the applet program according to the specific process requirements.
The following are the specific configuration settings:
② Hole Position Setting
a. Hardware Common Setting
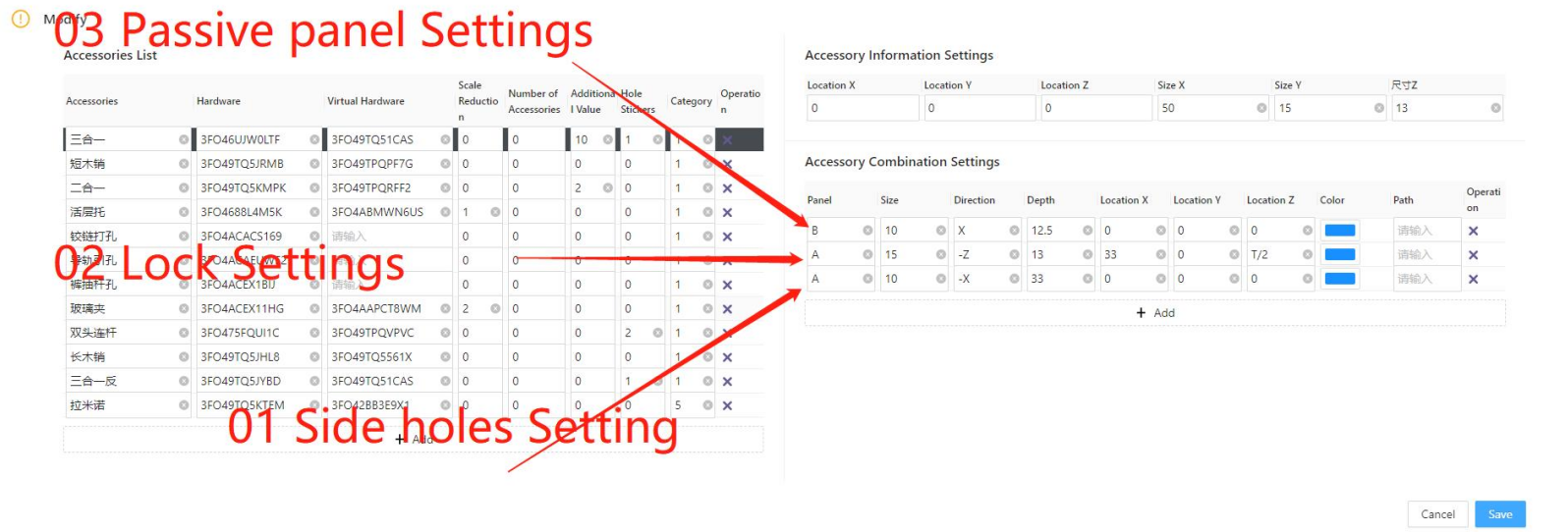
①:Panel 01 is set as the side hole exit mode of the active panel, and the connecting rod in the three-in-one is installed during the installation process. In this text, it is necessary to write its thickness hole exit rule, which is the position Z in the figure
② : Panel 02 is set as the empty hole mode of the lock pin outlet mode, and the eccentric wheel in the three-in-one is installed during the installation. In this paper, the depth value of the lock pin hole needs to be determined according to different panel thicknesses, that is, the depth in the figure
③ : Panel 03 is set as the passive panel outlet mode, and the threaded hole of the connecting rod (embedded part hole) in the three-in-one is generally installed during the installation process. In this paper, the value of the embedded part hole needs to be judged according to different panel thickness, and the purpose is to coincide with the center of the side hole of the 01-panel
b. Example
Note:
Centering: In the applet settings, it is considered as 0. A value of 0 represents the position at the center of the board thickness.
Offset 9: Offset 9 is commonly used for 25mm or 36mm boards, it should be set to T/2-9, which means placing the reference point on the board surface and shifting it down by 9mm for positioning.
Example:
Conditions: 18 panel is drilled in the center, 25 panel is drilled in the off-9 (T==22)OR(T==25)? (T/2-9):0
Panel 01 Formula: (T==25)? (T/2-9):0 Explanation: When the thickness of the panel is 25, the side hole is offset 9, otherwise, it is center drilling
Panel 02 Formula:Directly provide 13.5 Explanation: Since it is considered as an offset of 9 for drilling, the value should be written in its own standard format. In this case, it can also be calculated using a formula.
Panel 03 Formula:Same as “Panel 01 Formula”
1.2.4.4 Offset In Y Direction For Side Holes
① Commen Situation
Some hardware fitting in certain structures require multiple holes on the same surface. It can be analyzed as a side hole on the active panel, but the passive panel is composed of two holes, then it can be disassembled as:
Panel A: One side hole with a diameter of 10 and a depth of 36.
Panel B with two holes:
① Diameter: 12, Depth: 9
② Diameter: 10, Depth: 9
The center-to-center distance between these two holes is 8.
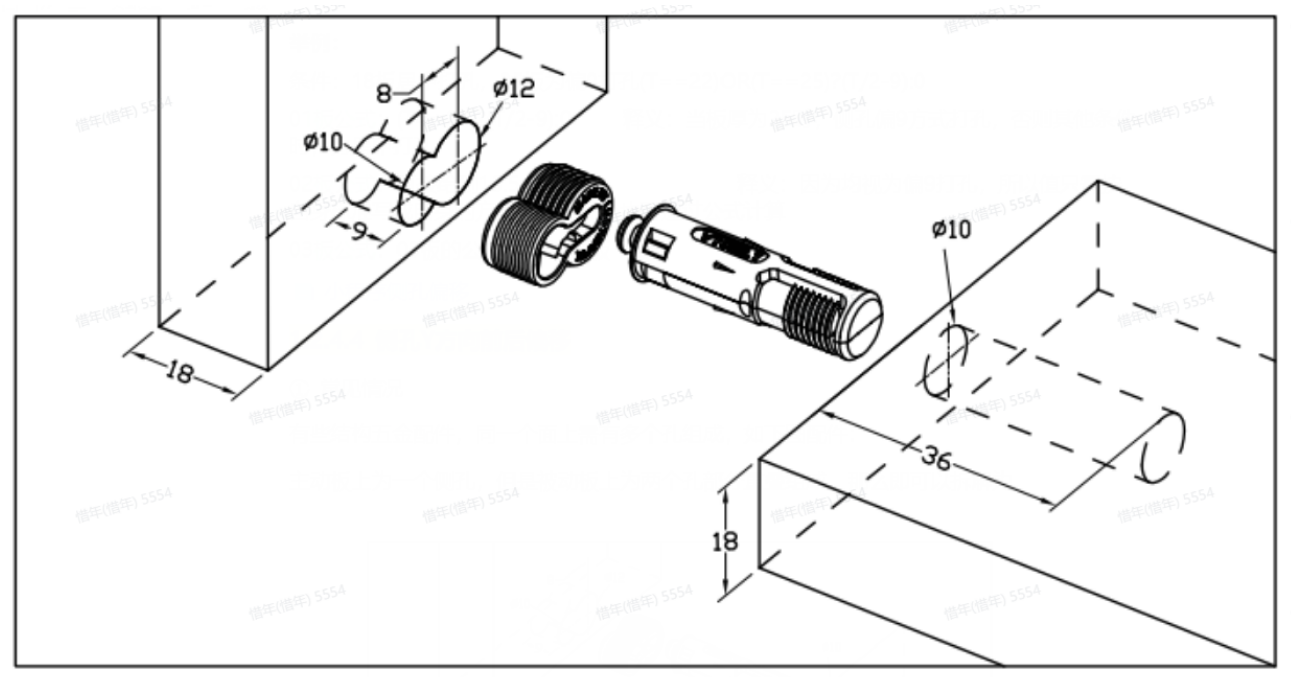
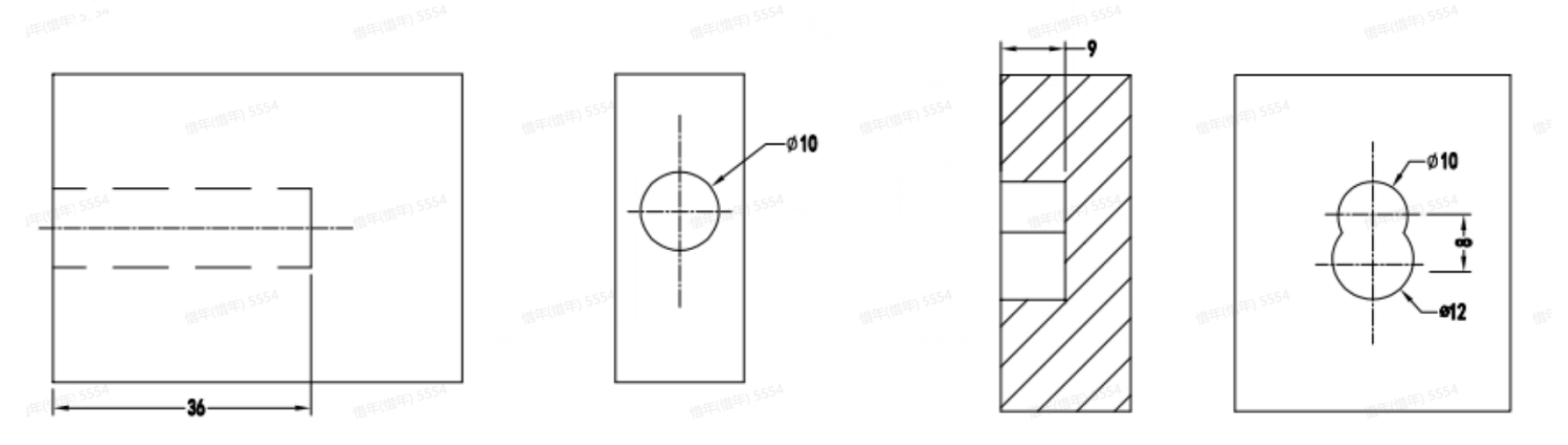
② Holes Position
According to the above, we need to configure this fitting as:
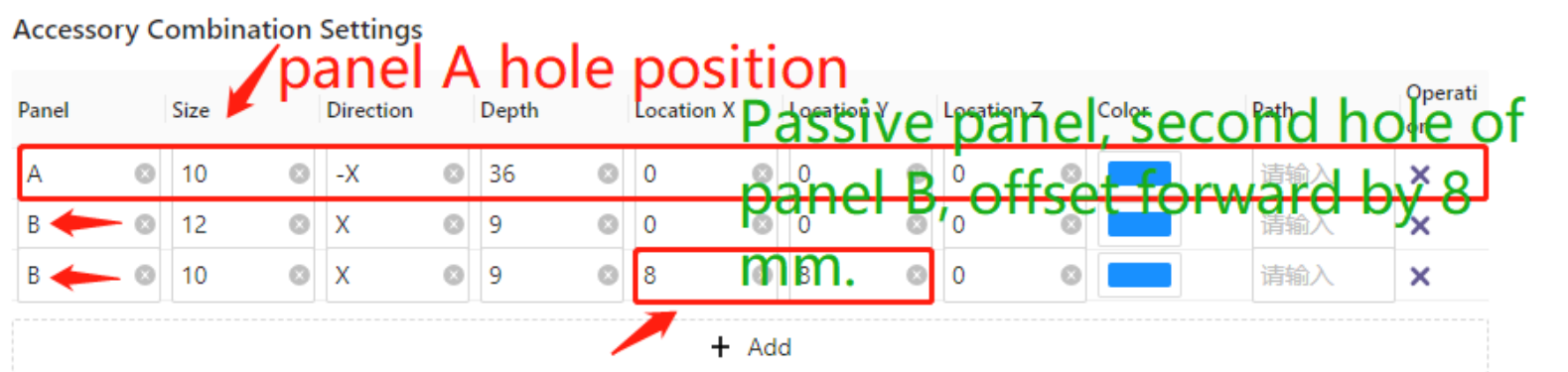
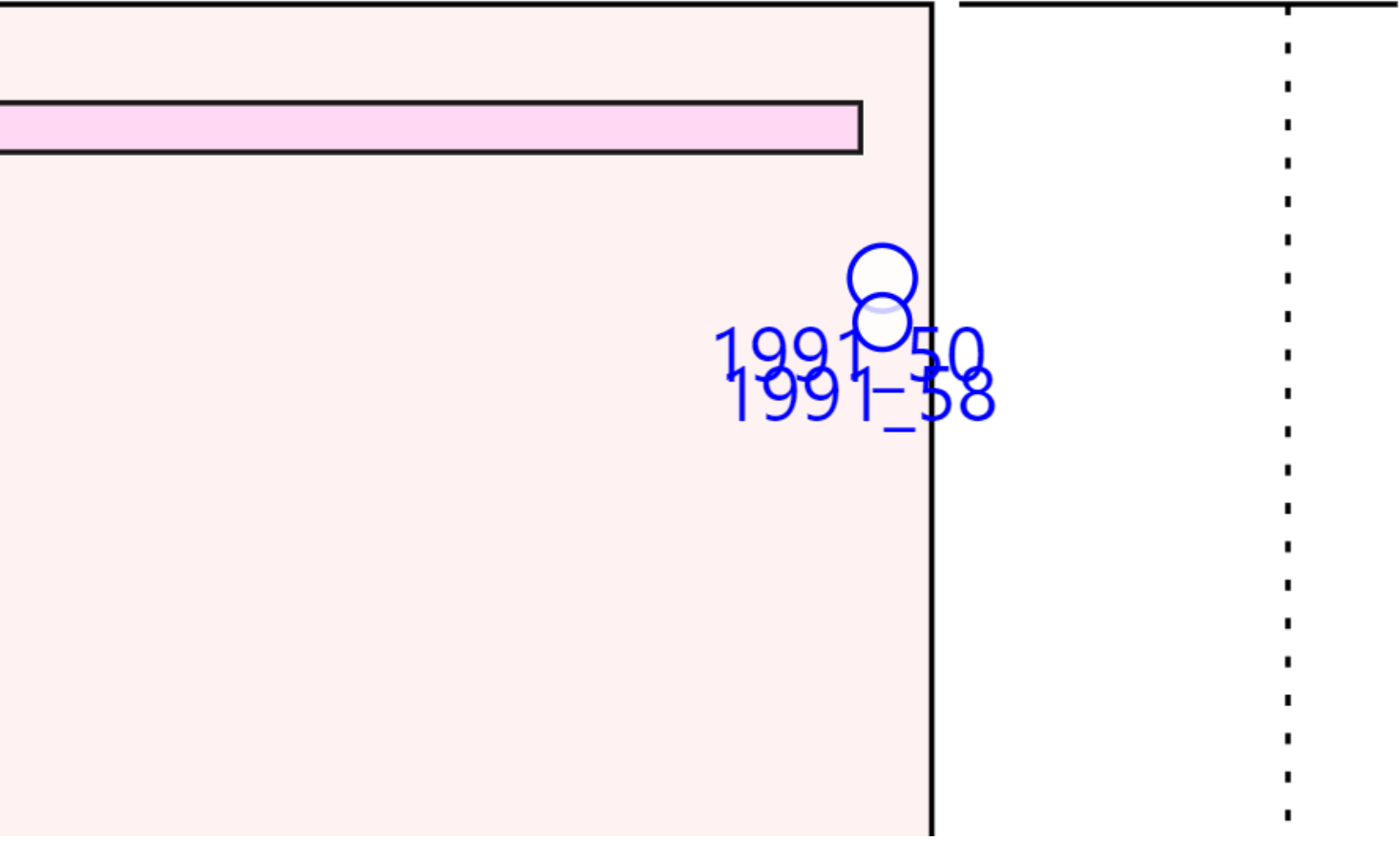
Note: For holes that require offset, the offset distance should be filled in both the X and Y positions with the same value. The sign (+/-) of the value determines the direction of the Y-axis offset. Positive value indicates forward, while a negative value indicates backward.
3、Hardware Slot Configuration
1.3.1 Hardware Slot Explanation
In the industry, there are many companies that use hardware such as strips and concealed handles, which typically require slots to be cut on the panel for installation. In Coohom, there are two ways to achieve this during the production output:
l Option 1: Create an auxiliary board and use the interference slot principle to achieve the required specifications by referring to the component docking technical standards;
l Option 2: Configure the slot in the applet by using a 3D model that generates collision surfaces. The slot type, size, and depth are determined based on the collision surface.
1.3.2 Hardware Slot Configuration
① Upload a 3D model that will generate collision surfaces during the design proces;
② In applet configuration, fill in the Product ID of the 3D model to ensure that the hardware slot matches the actual specifications of the hardware;
③ Define the data type for the hardware slot. Use type 1 for connecting hardware, type 2 for rectangular slots, type 3 for circular slots, type 4 for irregular slots, and type 5 for hidden component slots. Fill in the corresponding type value based on the required slot shape;
④ In the fitting information settings on the right side, fill in the corresponding hardware slot depth in the Z position;
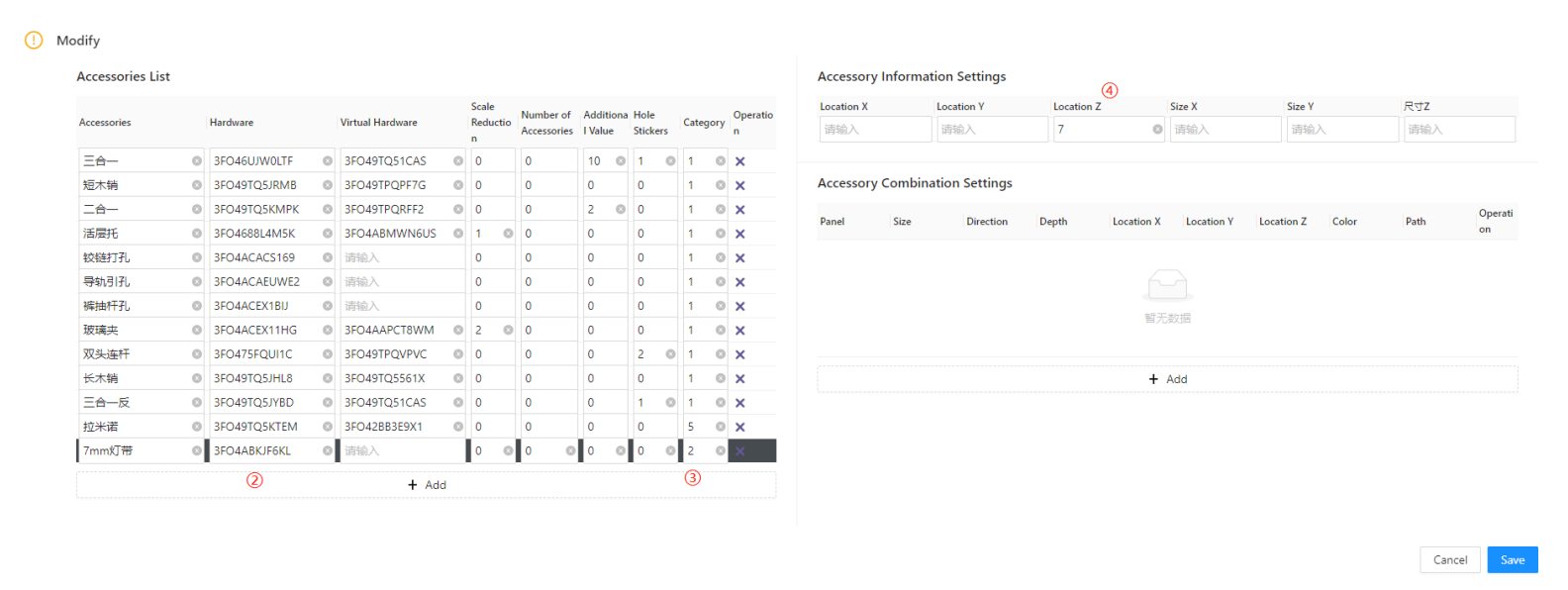
Note:
① In applet, the slot width and depth increments are not calculated for hardware slots. When the type is circular slot, the diameter will be defined as the minimum value of the length and width of the corresponding 3D model.
② When the required slot length and width or the specifications of the circular slot are less than 10, at least one side of the 3D model should have a length greater than or equal to 10. The other side can be set to the required slot width or the diameter of the circular slot. For example, if a diameter of 5 millimeters is needed for a circular slot, the 3D model dimensions should be written as 10*5. The system will define the diameter of the circle based on the minimum value of the two sides.
4、Hidden Condition Output
Hidden parts in the BOM disassembly, the overall implementation is as follows:

In disassembly software, the core information of the hidden part such as its name, slot specifications, orientation, etc., is written into the BOM. As for how this hidden component integrates with the layout and other systems, it is maintained by the ecosystem based on the core information in the BOM. In the applet configuration, we only need to configure this information.
1.4.1 Hardware Fitting Information
-
In the disassembly configuration, the hardware type is fixed as 5, then the system will write the accessory according to the standard defined by the hidden part when writing data.
In the disassembly configuration, the hardware type is fixed as 5, then the system will write the accessory according to the standard defined by the hidden part when writing data.
-
The fitting name will be written into the BOM according to the previously filled.
The fitting name will be written into the BOM according to the previously filled.
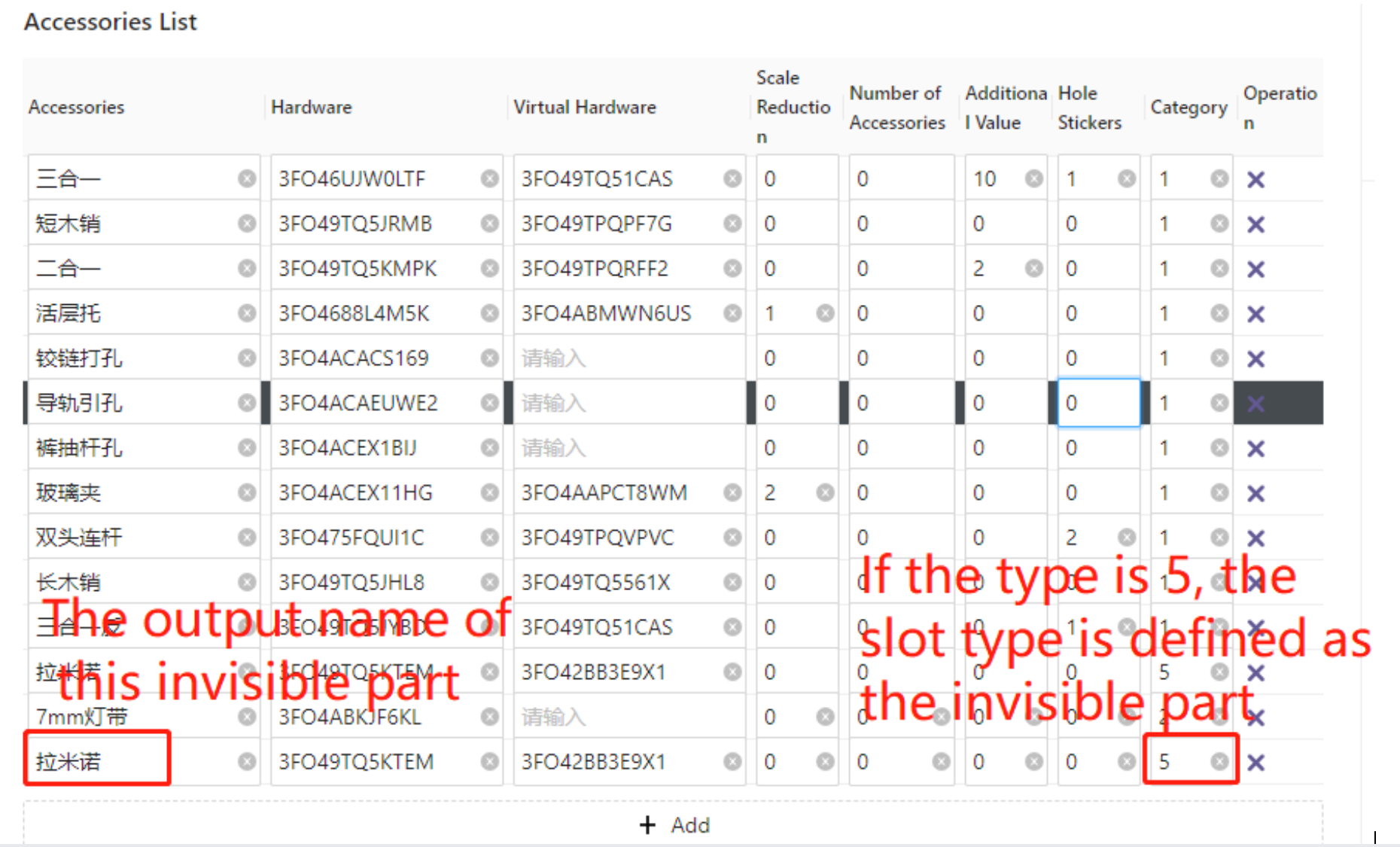
1.4.2 Fitting Slots Definition
After completing the information filling for section 4.1, we also need to provide the ecological software with information about the hidden slot. This information includes the slot width, slot depth, slotting direction on either A or B panel, and the slot length from start to finish.
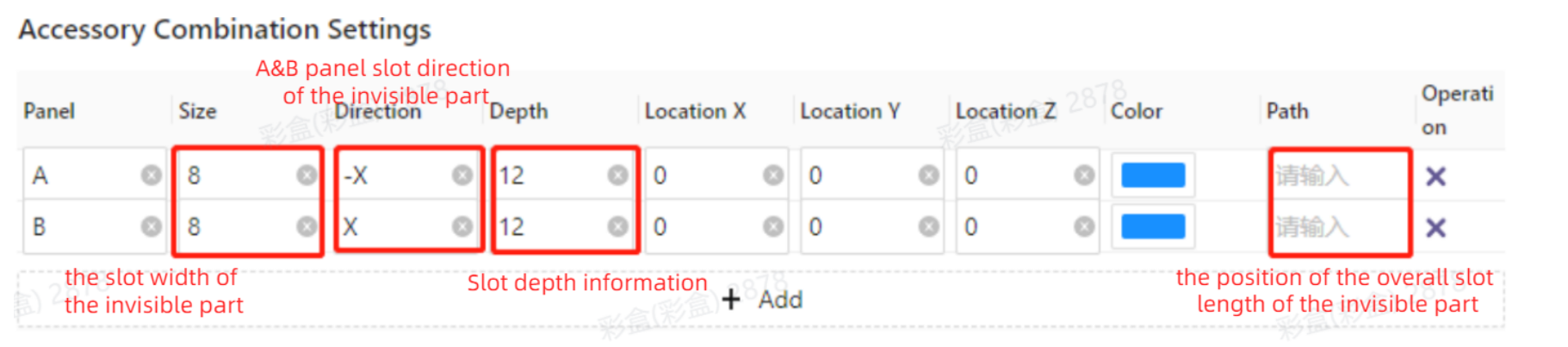
1.4.3 Tips
The configuration of hidden parts in applet only represents the ability to configure core information, but it does not mean that production is possible once configured. The production information depends on whether the backend ecological software is integrated with the hidden parts in the BOM (Bill of Materials), as well as whether the subsequent equipment in the ecological software can be connected for processing and other factors.
5、Edge Banding Configuration
In the disassembly Assistant, the edge banding docking method and component docking standard use the same approach. The name is filled in as "Used in Disassembly Assistant" and corresponds to the displayed name of the edge banding for the corresponding panel. The value is determined by the ET output values of the four edges of the board, and the thickness is based on the actual edge thickness value. This final calculation is included in the production data.